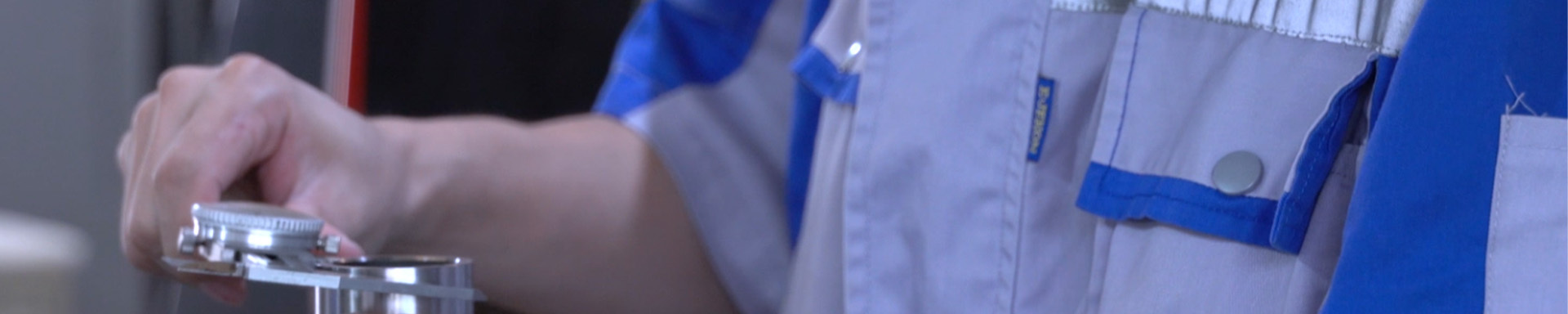
스텔라이트 21 / AMS5385G UNS R30021
2021-09-06 10:52Stellite 21 CoCrMo 합금(코발트-크롬-몰리브덴)은 코발트 기반 합금 중 하나이며 소위 스텔라이트 합금의 일종이기도 합니다. 내마모성과 내식성이 우수한 코발트계 합금입니다. 최초의 코발트계 합금은 코발트-크롬 2성분계 합금으로 개발되어 코발트-크롬-텅스텐 3성분계 합금으로 발전하였고, 이후 코발트-크롬-몰리브덴 합금이 개발되었다. 코발트-크롬-몰리브덴 합금은 코발트를 주성분으로 하는 합금의 일종으로 상당한 양의 크롬, 몰리브덴 및 소량의 니켈, 탄소 및 기타 합금 원소를 함유하고 때로는 철을 함유하기도 합니다. 합금의 조성에 따라 용접 와이어로 만들 수 있으며 분말은 단단한 표면 용접, 용사,
코발트와 크롬은 코발트 기반 합금의 두 가지 기본 요소이며 몰리브덴을 첨가하면 주조 또는 주조 후 더 미세한 입자를 얻을 수 있고 더 높은 강도를 얻을 수 있습니다. 코발트-크롬-몰리브덴 합금은 기본적으로 두 가지 범주로 나뉩니다. 하나는 일반적으로 주조 제품인 CoCrMo 합금이고 다른 하나는 일반적으로 (열간) 주조 정밀 가공인 CoNiCrMo 합금입니다. Cast CoCrMo 합금은 수십 년 동안 치과에서 사용되어 왔으며 현재는 인공 관절을 만드는 데 사용됩니다. 캐스트 CoNiCrMo 합금은 무릎 관절 및 엉덩이 관절과 같은 무거운 하중을 수용하는 관절을 만드는 데 사용됩니다. 그러나 CoCrMo 합금은 관절 임플란트 재료로서 인체에 이식된 후 Co, Cr, Ni 및 기타 유해한 이온을 방출합니다.
Stellite 21 화학 성분:
Stellite 21 기계적 특성:
용접성 분석
현재 국제적으로 성숙한 경험에 따르면 표면 층의 기능은 주로 표면 층의 용접 금속의 화학 조성과 희석 비율에 의해 결정되며 용접 금속의 화학 조성은 용접 재료의 화학 조성에 따라 다릅니다. . 용접 재료 선택 후 용접 금속의 화학 조성을 기본적으로 확인했습니다. 용접 공정을 선택할 때 외부 요인으로 인해 용접 금속의 화학적 조성 변화 또는 기타 불순물 원소의 침투를 방지하는 것을 고려할 필요가 있습니다. 희석률의 크기는 용접 중 입력 열(E)의 크기, 즉 열에 따라 다릅니다. 입력이 클수록 희석률이 높아집니다. 그렇지 않으면 감소 및 열 입력은 다음과 같이 계산됩니다.
공식에서 E는 용접 열 입력, J/mm입니다. 나는 용접 전류, A입니다. U는 용접 전압, V입니다. u는 용접 속도, mm/min입니다. 따라서 용접 공정을 선택할 때 표면층의 용접 금속의 화학 조성을 확보하고 용접 열 입력량을 줄이는 것이 필요합니다. 사전 확인된 공정 흐름 경로는 블랭킹→플래닝 및 밀링 비파괴 검사(PT)→예열→용접→육안 검사→비파괴 검사(PT)→시료 처리→화학 분석 및 기능 검사→재료 수집→결과 분석이다. → 정화 및 사용 생산 보고 (5) 0
용접 전 요구 사항
표면 용접의 표면에 균열, 기공, 중간층, 두꺼운 가죽 및 기타 표면 결함이 없는 것을 액체 침지 검사를 통해 확인한 후 표면 용접 표면을 아세톤으로 청소합니다. 표면 용접 품질 재료의 경우 표면 처리 부품을 15°C 이상으로 예열하십시오. 손이 만지고 따뜻해지면 용접이 즉시 수행됩니다. 동시에 용접 환경의 상대 습도가 80% 이하, 풍속이 2m/s 이하, Ar 가스 순도가 99.99%에 도달해야 함을 확인합니다.
용접 중 요구 사항
용접열입력(E)의 크기는 용접전류(I)와 용접전압(U)의 곱의 크기와 용접속도( v)는 반비례합니다. 비용융 전극 수동 아르곤 텅스텐 아크 용접(GTAW) 용접 방법의 경우 용접 전류는 사전 설정된 제어 가능한 요소에 기인하고 용접 전압 및 용접 속도는 인공 제어 및 임의 요소에 기인합니다. 이것은 프랑스 RCC-M 사양의 네 번째 부분에 있습니다. S권에서 인용"용접". 동시에 ISO 15614-7:2007의 8.5.4절에 설명되어 있습니다."금속 재료에 대한 용접 절차의 자격 파트 7: 오버레이 용접": 층별 승인 입열량 범위의 상한선이 용접절차 평가 이상임. 동일한 레이어에서 사용하는 입열량은 25%이며, 하한은 용접 공정을 평가할 때 같은 레이어에서 사용하는 입열량의 10% 미만입니다.
용접 전압과 용접 속도는 사람이 제어하기 때문에 용접 사양 매개 변수를 선택할 때 용접 전류의 크기를 제어하는 것이 우선입니다. 표면 용접의 품질을 보장한다는 전제하에 가능한 한 낮은 용접 전류 값을 선택하십시오. 즉,"작은 전류, 짧은 아크 용접, 빠른, 다층 다중 패스 용접". 용접 사양 매개변수 조정. 표면 용접시 비드 간격을 엄격하게 제어하십시오. 희석율을 최소화하기 위해 다음 비드를 이전 비드 너비의 절반으로 눌러야 합니다. 용접 패스 사이의 용접 방향은 용접 응력과 변형을 줄이기 위해 하나씩 앞뒤로 용접해야합니다. 용접하기 전에 용접 전원은 미리 공급된 아르곤 가스와 지연된 아르곤 공급 가스의 보호 상태로 미리 조정되어야 합니다. 처음에는 동일한 재료의 점화 아크 보드에서 전류를 조정하고 아크를 점화시킨 다음 용접을 용접을 시작하기 위해 용접 영역의 시작 부분으로 옮겨야합니다. 용접의 중심축을 따라 번호가 매겨진 6번 위치에서 시작하여 용접이 양쪽에 앞뒤로 용접됩니다. 크레이터 크랙이 발생하지 않도록 아크를 닫을 때 크레이터를 채워야 합니다. 용접 조인트는 용접 조인트의 조인트 품질을 보장하기 위해 리플 로우 아크 방식을 채택합니다. 각 용접 패스 사이의 용접 조인트는 엇갈려 있어야 합니다. 표면두께는 3.5~4.0mm 이내로 하여야 한다. 용접 후 암면을 사용하여 따뜻하게 유지하고 천천히 실온으로 식힙니다.
용접 단점 및 조치
용접 전과 용접 중 외관 마무리. 표면 산화 스케일, 오일 얼룩, 불순물, 중간층 코팅, 용융 슬래그 및 기타 유해한 불순물을 철저히 제거하여 표면 표면이 매끄럽고 윤활되며 금속 광택이 있고 균열, 기공, 슬래그 개재물 등과 같은 결함이 없는지 확인하십시오. 표면에;
용접 전 예열, 패스 간 온도 제어, 용접 후 서냉을 포함한 용접 중 온도 제어. 용접 전 예열 및 용접 후 느린 냉각은 용접 후 냉각 속도를 줄이고 유해한 온도 구배로 인한 잔류 응력의 일부를 줄일 수 있습니다. 층간 온도 제어는 고온 체류 시간을 줄이고 용접 조인트의 거친 결정 취성을 방지하며 충격 인성을 감소시킬 수 있습니다.
용접 후 응력 제거 열처리. 표면 처리가 완료된 후 내부 구속 응력이 커서 단순히 균열이 발생합니다. 응력 제거 열처리를 통해 내부 응력을 적시에 제거하여 결함이 발생하지 않도록 할 수 있습니다.